Services
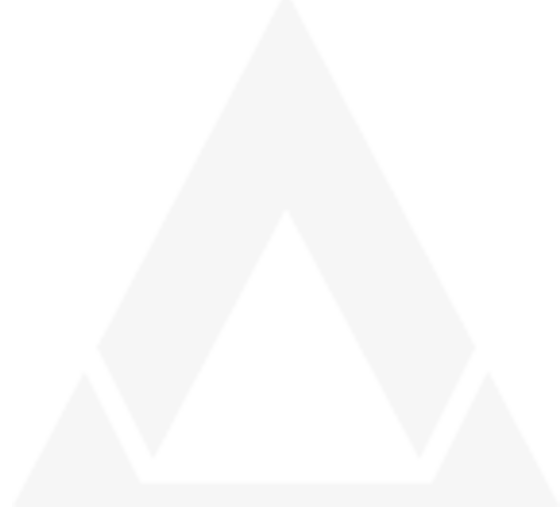
About Us
MORE
Beijing Guoshi Ankang Technology Co., Ltd. is a professional safety technical service organization established in 2006. We have been engaged in safety technical consulting services for 20 years. The company has 95 employees, including 45 full-time appraisers, 20 first-level appraisers, 12 second-level appraisers, 13 third-level appraisers, 14 registered safety engineers, 25 senior engineers and above. We also have an independent technical expert team including 75 people and 9 certified safety engineers from Germany Rhine TUV. Since its establishment, the company has provided safety evaluation and safety technical consulting services to domestic and international petrochemical companies such as Sinopec, China Petroleum, China Chemical Industry, CNOOC, China Energy (China Coal, Guodian), Wanhua Group, BASF, Bayer, Hunsman, American AP, Shell and other domestic and international petrochemical companies. The service business areas include safety evaluation, HAZOP analysis, SIL analysis, QRA analysis and calculation, etc. In February 2020, the "Safety Evaluation Agency Qualification" certificate renewal business scope includes: land oil and natural gas mining industry; onshore oil and gas pipeline transportation industry; petroleum processing, chemical raw materials, chemicals and pharmaceutical manufacturing industry; metal smelting, etc.
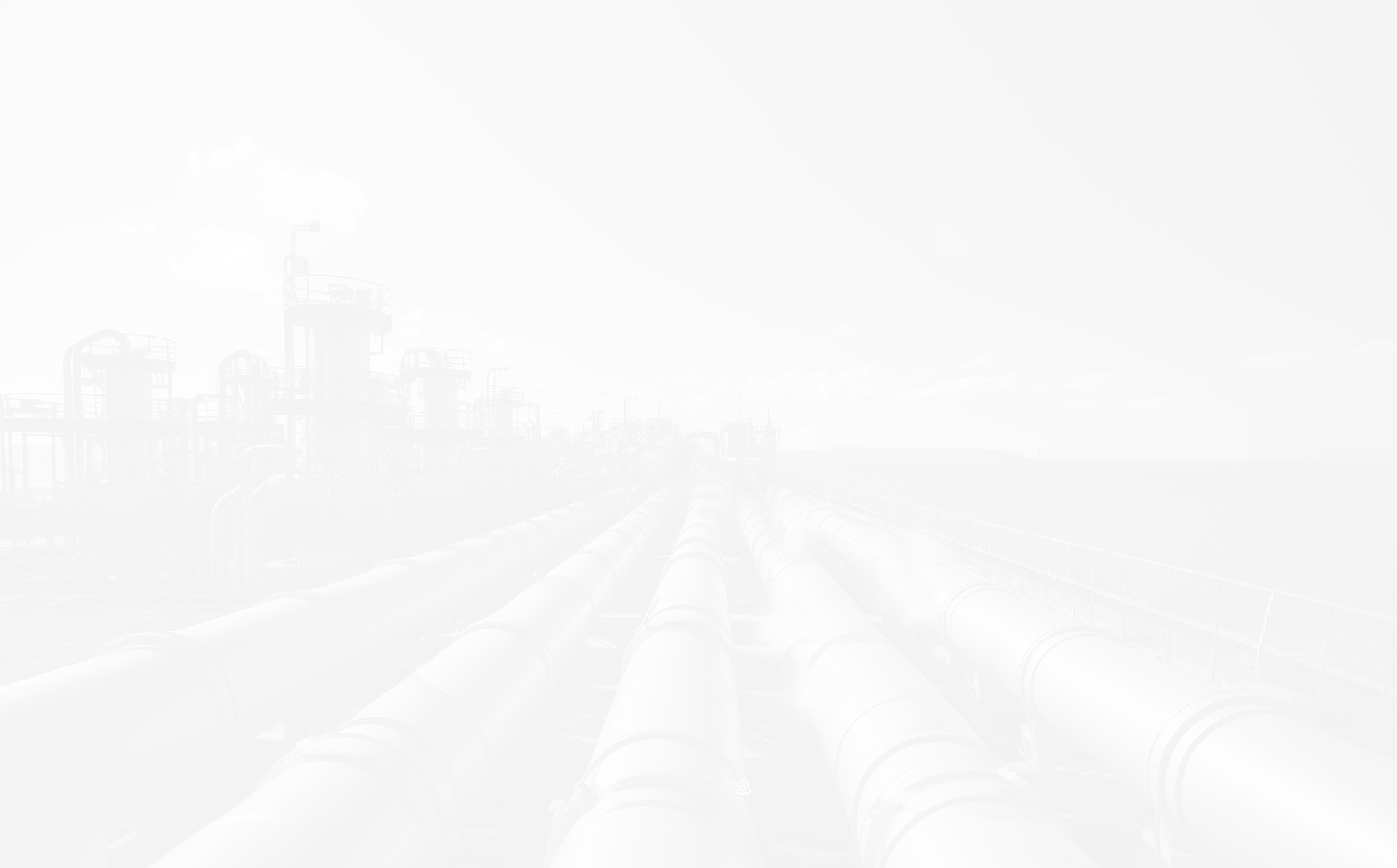
Business coverage area
News Center